COOPER SA has all the necessary facilities at its disposal in order to ensure optimal production conditions in strict accordance with the requirements of the Good Manufacturing Process (GMP) Guidelines.
The National Organization for Medicines (NOM) has granted COOPER SA license to produce of pharmaceutical products for human use having established that its manufacturing facilities meet all relevant legal requirements (national and European).
NOM regularly inspects all production, packaging, quality control, warehousing and distribution operations of the company in accordance with European legislation.
The production stages of COOPER SA products, in accordance with good manufacturing practices, are the following:
- Purchase of raw ingredients
- Purchase of packaging materials
- Production
- Quality control for release
- Warehouse storage
- Controls and tests pertaining to the previous stages
The activities of our production in detail are as follows:
Sterile Products:
1. Liquid pharmacotechnical forms (large volume parenteral solutions):
i) sterilized with the completion of the process
2. Liquid pharmacotechnical forms (small volume parenteral solutions):
i) Aseptically manufactured
ii) sterilized upon completion of the process with a final sterilization
iii) Sterile ophthalmic solutions
3. Solid pharmacotecnhical forms
i) Dry injectable penicillin-containing
i) Dry eye drops penicillin-containing
Non-sterile products:
1. Liquid pharmacotechnical forms (oral solutions, enema)
Formulation of medicines COOPER SA:
- Ocular use
- Nasal use:
- Rectal use:
- Parenteral use
- Liquid oral solutions
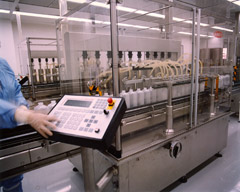
In 1977, COOPER SA, using its extensive technical expertise and skilled scientific staff, created a sterile chamber complex with multiple Class A/B chambers. Sterile chambers meet the latest requirements for manufacture of sterile products in the form of liquid injectables in vials and ampoules.
The production output of the sterile facilities is supported by two fully-equipped class C preparation rooms which contain: washing machine for vials, production plant for water for injection, two Class A dry two-door sterilizing ovens, two liquid two-door sterilizing ovens fed by a clean steam generator, a device for optical control of liquids, injectables and TOC testing device for distilled water, a vial filling machine and an ampoule filling machine.
The sterile production areas of the plant are:
- A sterile area for the production of liquid large volume parenteral solutions
- A sterile area for the production of liquid small volume parenteral solutions and sterile ophthalmic solutions
- A sterile area for the production of dry penicillin-containing injectables and eye drops
- Clean areas for manufacturing liquid oral solutions and solutions for enemas
State-of-the-art facilities, expert staff, and the strict observance of all manufacturing and sanitary standards are a guarantee of the ideal result.
The WFI used in production is prepared daily at COOPER SA through distillation of deionized water (purified water produced by Reverse Osmosis – RO).
Deionized water (purified water) produced by RO, is used to supply the production system with distilled water.
The quality of water produced is monitored daily by the Quality Control Department. Distilled water which does not meet specifications is automatically rejected.
Supply to the system is not always sufficient for production operations (Qf~ 4 m3/h). The installation is automatically sterilized when not in operation for any extended period of time, and before operation is restarted, e.g. following holiday periods.
It should be noted that the production of Water for Injections (WFI) in this way (carbon bed-softener-RO-multiple distillation) is in compliance with the requirements of the European Pharmaceutical Industry.
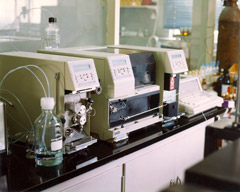
COOPER SA has all the necessary facilities at its disposal in order to ensure optimal production conditions in strict accordance with the requirements of the Good Manufacturing Process (GMP) Guidelines.
The National Organization for Medicines (NOM) has granted COOPER SA license to produce of pharmaceutical products for human use having established that its manufacturing facilities meet all relevant legal requirements (national and European).
NOM regularly inspects all production, packaging, quality control, warehousing and distribution operations of the company in accordance with European legislation.
The production stages of COOPER SA products, in accordance with good manufacturing practices, are the following:
- Purchase of raw ingredients
- Purchase of packaging materials
- Production
- Quality control for release
- Warehouse storage
- Controls and tests pertaining to the previous stages
The activities of our production in detail are as follows:
Sterile Products:
1. Liquid pharmacotechnical forms (large volume parenteral solutions):
i) sterilized with the completion of the process
2. Liquid pharmacotechnical forms (small volume parenteral solutions):
i) Aseptically manufactured
ii) sterilized upon completion of the process with a final sterilization
iii) Sterile ophthalmic solutions
3. Solid pharmacotecnhical forms
i) Dry injectable penicillin-containing
i) Dry eye drops penicillin-containing
Non-sterile products:
1. Liquid pharmacotechnical forms (oral solutions, enema)
Formulation of medicines COOPER SA:
- Ocular use
- Nasal use:
- Rectal use:
- Parenteral use
- Liquid oral solutions
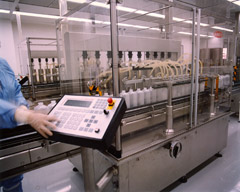
In 1977, COOPER SA, using its extensive technical expertise and skilled scientific staff, created a sterile chamber complex with multiple Class A/B chambers. Sterile chambers meet the latest requirements for manufacture of sterile products in the form of liquid injectables in vials and ampoules.
The production output of the sterile facilities is supported by two fully-equipped class C preparation rooms which contain: washing machine for vials, production plant for water for injection, two Class A dry two-door sterilizing ovens, two liquid two-door sterilizing ovens fed by a clean steam generator, a device for optical control of liquids, injectables and TOC testing device for distilled water, a vial filling machine and an ampoule filling machine.
The sterile production areas of the plant are:
- A sterile area for the production of liquid large volume parenteral solutions
- A sterile area for the production of liquid small volume parenteral solutions and sterile ophthalmic solutions
- A sterile area for the production of dry penicillin-containing injectables and eye drops
- Clean areas for manufacturing liquid oral solutions and solutions for enemas
State-of-the-art facilities, expert staff, and the strict observance of all manufacturing and sanitary standards are a guarantee of the ideal result.
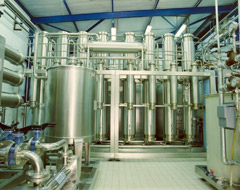
Το απιονισμένο νερό (purified water) που παράγεται από την RO, χρησιμοποιείται για την τροφοδοσία του συστήματος παραγωγής απεσταγμένου νερού.
The WFI used in production is prepared daily at COOPER SA through distillation of deionized water (purified water produced by Reverse Osmosis – RO).
Deionized water (purified water) produced by RO, is used to supply the production system with distilled water.
The quality of water produced is monitored daily by the Quality Control Department. Distilled water which does not meet specifications is automatically rejected.
Supply to the system is not always sufficient for production operations (Qf~ 4 m3/h). The installation is automatically sterilized when not in operation for any extended period of time, and before operation is restarted, e.g. following holiday periods.
It should be noted that the production of Water for Injections (WFI) in this way (carbon bed-softener-RO-multiple distillation) is in compliance with the requirements of the European Pharmaceutical Industry.